NEST3D: il nuovo modo di stampare “tra le righe”
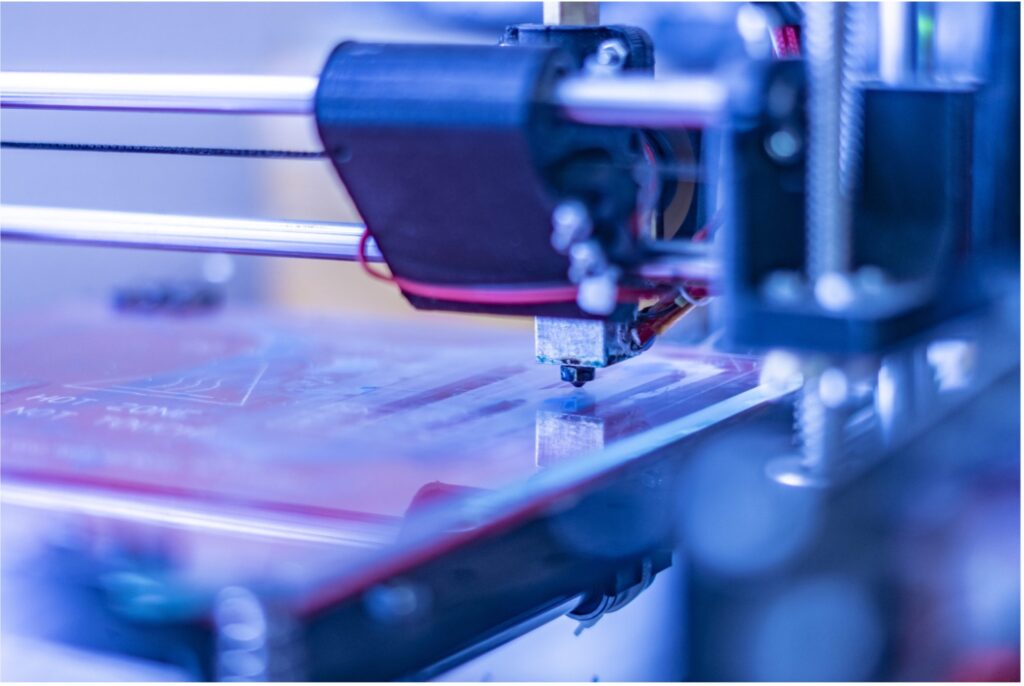
Ancora una volta la protagonista è lei, la stampa 3D, tecnologia tanto attuale quanto promettente ed in continua evoluzione. Già diverse volte ci siamo soffermati sulla versatilità e sull’incredibile vantaggio che questo tipo di tecnologia riesce ad apportare non soltanto nel campo biomedicale e tessutale, dove ormai viene impiegata su svariati livelli, ma anche quello meccanico, nel design, nella moda e persino nella gastronomia. Una nuova strada potrebbe essere NEST3D.
Economica, rapida, ideale nelle produzioni customizzate, quali limiti porta, attualmente, con sé?
Sicuramente uno dei principali ostacoli che si incontra, quando si ha a che fare con la stampa 3D, è riuscire ad ottenere strutture di biomateriali molto complesse e ad altissima risoluzione. Questo vale sempre? Non è detto.
Attualmente, infatti, le tecniche di fabbricazione per questo tipo di impieghi esistono e sono quelle basate principalmente sulla fotopolimerizzazione, ovvero sull’utilizzo di luce, proprio perché consentono di generare strutture complesse ad alta precisione in geometrie non vincolate (basti pensare ad una SLA o una DLP).
Tuttavia, queste tecniche operano utilizzando resine liquide e sostanze chimiche altamente specifiche, per cui i materiali in genere richiedono una funzionalizzazione e un’attenta messa a punto per essere resi processabili. Questo, a sua volta, può comportare una compromissione dei requisiti funzionali richiesti del biomaterale, con il rischio che essi incidano sulle performance del modello atteso.
D’altro canto, però, sfruttare le tecniche di estrusione è incredibilmente limitante, se pensiamo a strutture così complesse e alla loro risoluzione. Con le normali stampanti per estrusione FDM, le dimensioni minime delle caratteristiche ottenibili con i materiali termoplastici sono pressoché simili a quelle dell’ugello usato, pertanto raggiungere una scala dimensionale inferiore a quella millimetrica rimane una sfida importante.
È in questo contesto che si inserisce NEST3D, interpretabile come un connubio tra il processo additivo e lo stampaggio a iniezione, ma che supera diversi limiti di entrambe le tecniche. L’idea alla base di NEST3D è che si può realizzare un oggetto, dalla geometria discretamente complessa, sfruttando lo spazio “negativo” tra le linee stampate. Il modello negativo in una struttura che viene stampata in 3D può permetterci di arrivare a delle geometrie che, altrimenti, sarebbero impossibili da ottenere con uno stampaggio ad estrusione diretta, anche con l’uso di materiale di supporto.
NEST3D: come si ottiene il modello negativo?
Tale modello si ottiene attraverso la colata a pressione di un materiale secondario e dissolvendo poi il modello estruso. Questo ci permette di utilizzare una stampante FDM, non necessariamente professionale, e di creare ugualmente oggetti 3D ad alta risoluzione con elementi strutturali orientati in maniera arbitraria, sfruttando un’ampia gamma di biomateriali. Questo consente di generare scaffold per l’ingegneria tessutale che siano degradabili, porosi (fino al 97%) e con rigidità regolabile su tre ordini di grandezza.
Negli esperimenti condotti dagli ideatori di NEST3D, è stato scelto il polimero PVA come materiale da estrudere, perché solubile in acqua ed ampiamente utilizzato nella tecnica FDM. In più, ci si aspettava che i modelli stampati fossero sufficientemente rigidi per colare, al loro interno, materiali ad alta viscosità. I ricercatori hanno elaborato una strategia di stampa del modello negativo all’interno di un modello cuboidale standardizzato, compresi i fori di ingresso (per il materiale fuso) e i fori di uscita (per consentire la fuoriuscita dell’aria intrappolata).
Il materiale da colare scelto è stato il PCL, che è uno dei polimeri più usati nell’ingegneria biomedica, sia in ambito clinico nelle suture, sia nella somministrazione di farmaci, sia nella costruzione di scaffold. Il PCL è stato portato al di sopra della sua temperatura di fusione (60 °C) e colato all’interno del modello come liquido viscoso.
Nella stampa NEST3D, diversamente da quanto avviene nella normale FDM, la risoluzione è determinata dalla spaziatura tra due linee depositate, quindi l’idea di superare il vincolo della dimensione dell’ugello dipende proprio da questa assunzione.
Infatti, con questo sistema, si ottiene uno spessore minimo della parete verticale di circa 140 µm, usando un ugello con apertura da 400 µm. Il risultato è una gamma di oggetti prodotti il PCL, dalla complessità geometrica notevole, di piccolissime dimensioni e ad alta risoluzione.
È importante sottolineare che la tecnica di stampa NEST3D è eseguibile avendo a disposizione una comune stampante 3D FDM e materiali di laboratorio comunemente reperibili, un fattore non da poco che può contribuire all’utilizzo in larga scala della ricerca nei campi della produzione additiva e dell’ingegneria tessutale.
In conclusione, con la stampa NEST3D abbiamo la capacità di produrre strutture 3D con una complessità che, altrimenti, sarebbe auspicabile solo con tecniche di fabbricazione basate sulla luce, godendo di una straordinaria gamma di materiali utilizzabili.
A cura di Nicole Rinaldi